Lets try and put a new perspective to this matter.
The issue that Tyre Bands seek to address is the chance the tyre bead may disengage from the bead seating position of the wheel rim, and slip into the well of the rim.
Let's first consider what normally stops this from happening, and it's the pressure of the air inside the tyre which exerts thrust against the inside wall pushing the bead outwards. The the bead seat constrains it.
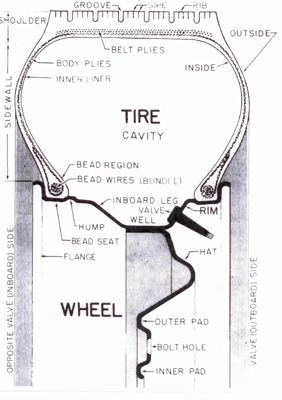
I'm sure you have watched a new tyre being fitted to one of your rims, you should have seen the fitter introduce the tyre to the wheel rim, and having used considerable force (produced by a machine) the tyre was eventually within the flanges but slightly loose.
The fitter then introduce compressed air through the valve port which is only used for a few seconds and the tyre expands but still does not quite fully jump the rim humps. A few more seconds of compressed air and by the air pressure alone, or sometimes with some physical encouragement of a sharp knock, the tyre will POP twice as the beads jump the humps and engage in the bead seats of the rim. By this time the pressure is probably up to 10 to 15PSI.
To get an idea of how much force the air has had to exert to get the beads into the seats, you need to calculate the side wall surface area multiplied by the air pressure at the time. Suffice to say for a 16 inch wheel rim with a tyre with a 4" tall side would have a tyre side wall surface area of all the in its in the order of 251 square inches. If the pressure was 10 PSI that gives a thrust load of 2510 Lbs of just about a ton, or more, if the pressure was higher.
The importance of this is it shows how much lateral force is needed to get the bead to jump over the hump during fitting.
Once in place, the bead is not only held by the bead seat but also has the assistance of the air pressure inside the tyre which at working pressure could be 30PSI or roughly 3 times the fitting pressure. This means it would need about 4 times the assembly thrust to cause the bead be dislodged from the seat whilst the tyre is inflated.
If the internal pressure drops, the the lateral force needed to move the bead diminishes but it will never fall below the assembly thrust. So even with a total loss of air pressure containment in a tyre, you would still have to generate a lateral force of about a ton to cause a bead to jump out of its seat.
High angle steering inputs at speed, or mounting a kerb or some other surface discontinuity might generate enough load, but basically if a normal driver becomes aware of a flat tyre, they shouldn't be using high speeds or large turning inputs that might generate these sorts of loads. As there is no need for such large lateral loads the risk of a tyre bead disengaging from the bead seat is very very small and it doesn't warrant the fitting of tyre bands to prevent it.
From my perspective the manufacturers have a product which can be justified for some emergency or military vehicles, but not for ordinary drivers. However, the makers have sought to spread negative rumours that prey on most drivers natural concerns about acquiring a flat tyre whilst driving. Most drivers do not have the scientific or mechanical understanding to rationalise the realities of such events, so the apparent risk is enough for some to fit tyre bands. even though the design of modern wheels and tyres, a tyre band offers no additional safety benefit for normal drivers.
At least, if a driver feels they need to have tyrebands fitted, it's not going to reduce safety, All it does is waste money, reduces payload of the vehicles, and can cause inconvenience when having tyres changed.